Based on available information these were some of the materials & manufacturing challenges of the SCE-200 engine project:
Low Pressure Oxidizer Turbopump (LPOT):

The Low-Pressure Oxidizer Turbopump (LPOT) was one of the 1st major sub-assemblies to be manufactured. This turbopump is used to feed the main turbopump with LOX. Initially the materials & manufacturing process used here were the same as those used in our cryogenic engines.
The LPOT was initially made of AISI-202, AISI-301 & AISI-316L grades of austenitic stainless steel. AISI 202 austenitic stainless-steel exhibits an impressive combination of toughness & corrosion resistance and is thus used for making impellers for driving LOX at 20 K. AISI 301 & 316L stainless steel can be hardened to tensile strengths of over 2000 MPa due to phase transformation of the unstable austenite into martensite.
Material selection/production for the LPOT was not a big challenge as LPSC could draw upon their experience of developing hydrolox engines. The problem was with the thin-walled bypass tubes that were joined using conventional welding & brazing (Look at pic above).
Austenitic stainless steels tend to have low yield strength. This wasn't a big issue for our hydrolox engines as they produce significantly less thrust & operate at significantly lower pressures. Adding to the problem was the conventional welding/brazing process used to manufacture these tubes. The conventional method was causing a higher than desirable impurity inclusion levels. These inclusions in the weld would create weak spots from where material failure would start.
To overcome these problems various commercially available precipitation hardened martensitic stainless steels with BCC structure were studied. Among the various alloys studied 14-5PH, A286, 11Cr-9Ni & 12Cr-10Ni grades were found to be suitable for our application. Subsequently domestic manufacturing for these grades of steel has been established in co-operation with MIDHANI, SAIL & DMRL.
Vacuum melting is now being used to significantly reduce the impurity levels of the alloys. Also, vacuum brazing methods have been adopted to minimize impurity inclusion during the joining process.
Low Pressure Fuel Turbine (LPFT):

While making the LPFT LPSC had encountered a different set of challenges. The design of the LPFT was much more intricate with complex vanes, internal cavities etc. The internal cavities have to be manufactured with precision & with good surface finish. As such lost-wax investment casting method was adopted to manufacture many of the LPFT's parts. The material chosen was Ti-6Al-4V alloy. The alloy has excellent corrosion resistance, it is also lightweight & has very high strength.
The only other organization in India that can produce high-precision super-alloy parts using lost-wax investment casting is DMRL. DMRL uses this type of casting to produce jet engine blades for the Kaveri program. Subsequently, DMRL's help was sought to produce a large number of parts for the SCE-200 engine. Most of the turbine housings including that of the main turbopump are made using this method.
Some parts, however, just could not be made using investment casting:
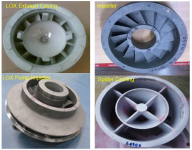
The surfaces of these parts were found to be unacceptably porous. These surface pores often act as the starting points for corrosion, followed by embrittlement & eventually failure. The SCE-200 engine is supposed to operate for a nominal duration of 355 seconds. These parts wouldn't survive that long.
So conventional machining was tried:

The machined parts worked fine. But the manufacturing cost & time were 2 major drawbacks. Then Laser Powder Bed fusion 3D printing was used to make these parts. Wipro 3D was contracted to do the 3D printing work.
3D printed LPFT straightener & nozzle tip made using Ti-6Al-4V alloy:
3D printed closed impeller is used in the fuel delivery system. It is made of AlSi10Mg alloy:
All of these sub-assemblies were tested & validated individually. After that, all the sub-assemblies have been combined to form the Power Head Test Article:

The PHTA is basically the SCE-200 engine without the nozzle. This has to be tested & validated before completely integrated engines start testing. This is the last major obstacle that we have to overcome to complete this project.
It is hard to overstate the kind of infrastructure, metallurgical expertise, manufacturing capability etc. this single project has created. None of this existed before this project came about. Thus, the schedule of this project suffered greatly. However, the benefits of the groundwork laid by this project would be enjoyed by other engine development projects that come after it.
Look at the 2 upcoming Methalox engines. One of them is a 200kN class & the other a 1000kN class. Those projects were announced publicly only a few of years ago. The 200kN engine has been fabricated & started hot testing a year ago. The 1000kN engine has completed preliminary design phase & will likely start detailed design soon. Both of those engines will benefit from the capacity built-up during the SCE-200 development.